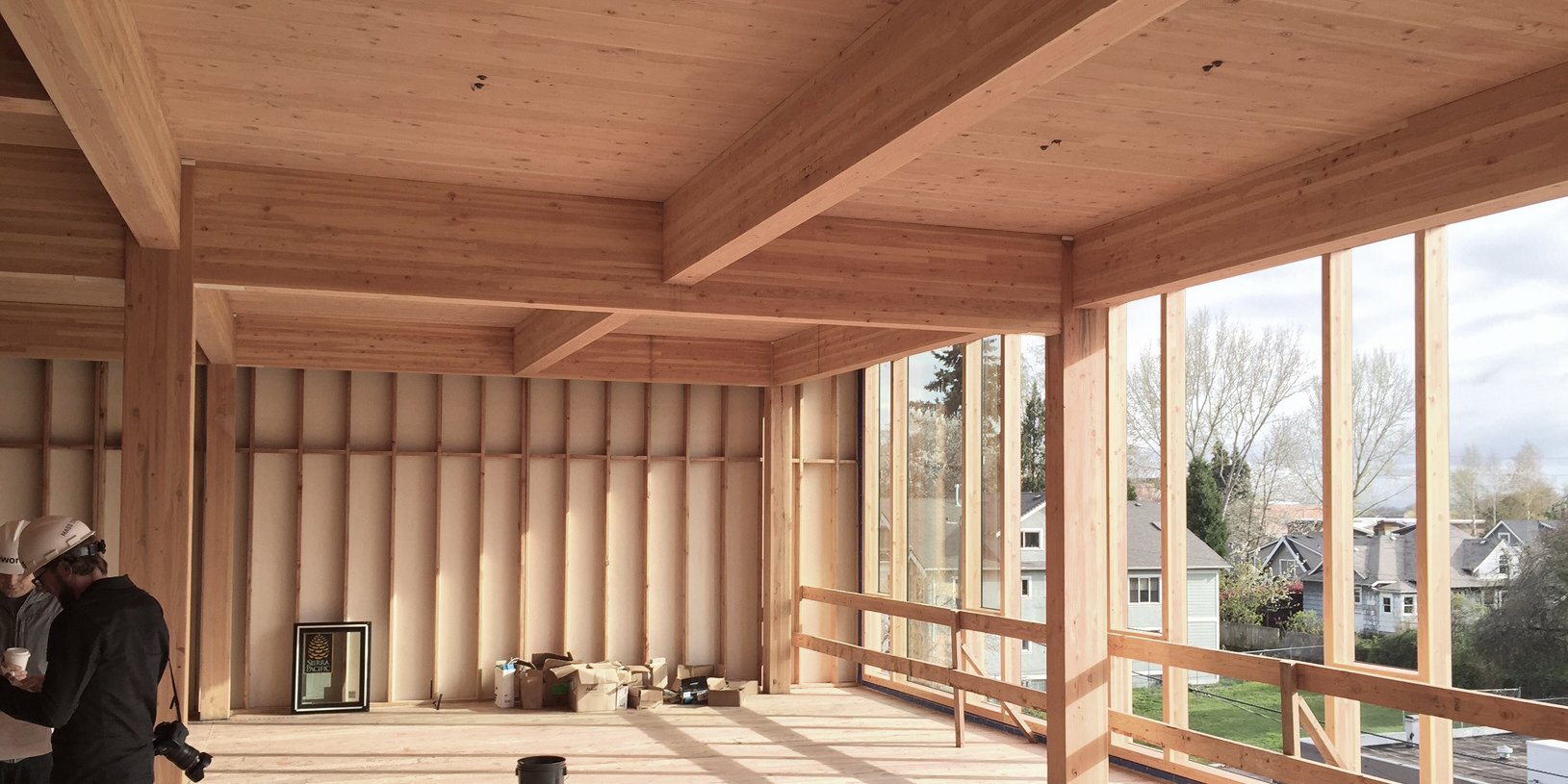
CLT is an engineered wood panel product made from layers of lumber glued together in alternating directions. Due to the perpendicular orientation of each layer, CLT is dimensionally stable and very rigid, allowing it to be used as floor slabs, load-bearing walls, and shear walls in mid- and high-rise construction. The boards in a CLT panel are glued together using a large hydraulic press. CLT is produced in a range of thicknesses and panel sizes. The most common panel types are three-ply, five-ply, and seven-ply. Panels are typically 10' wide and can be produced in lengths exceeding 40'. CLT technology originally developed in Europe during the 1990s, and in recent years its popularity in the US continues to grow.
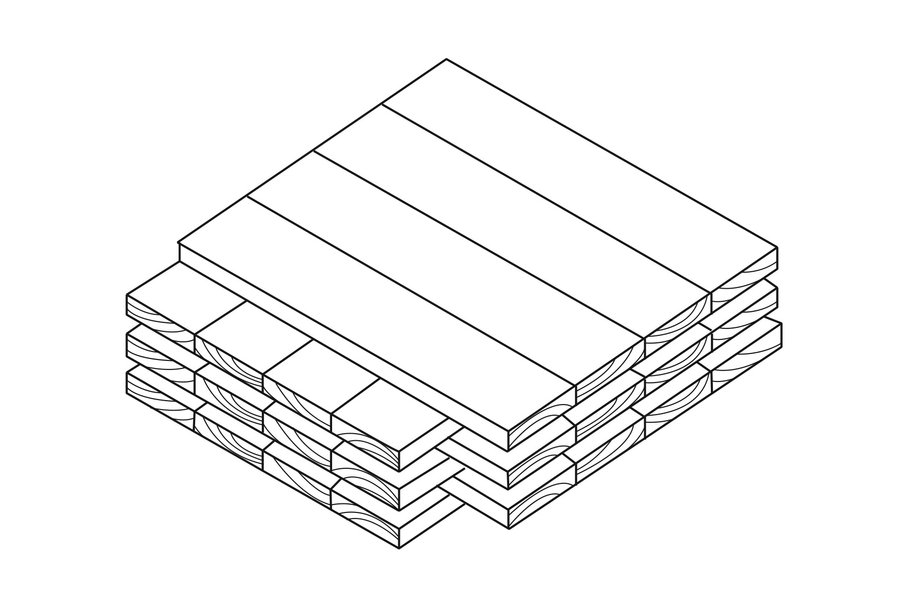
CLT is an engineered wood panel created by bonding together layers of wooden boards. The perpendicular orientation of the wood layers gives each panel its strength.
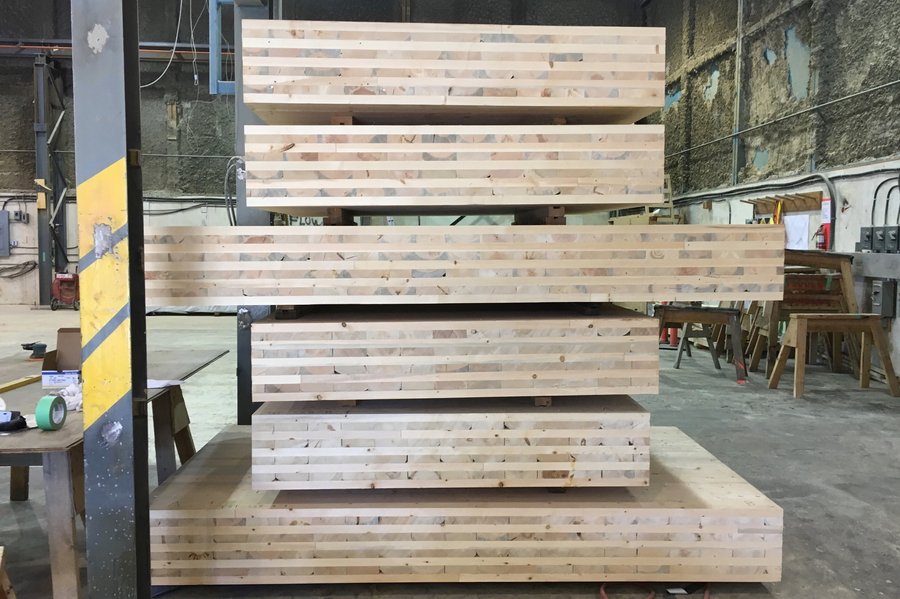
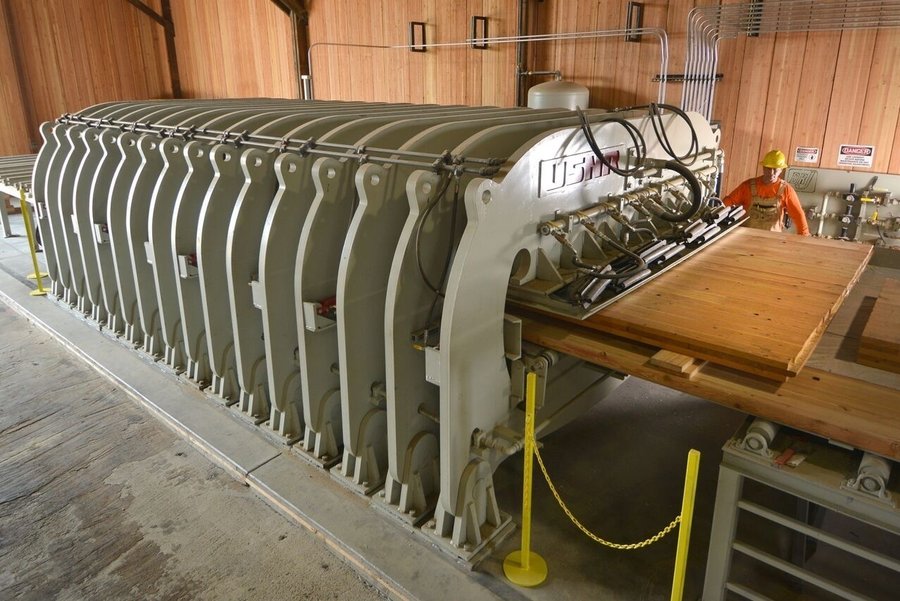
A CLT panel being manufactured on a hydraulic press at DR Johnson Lumber Co in Riddle, Oregon. Both the glulam columns and beams and CLT panels used to constructed Albina Yard were produced by DR Johnson Lumber Co.
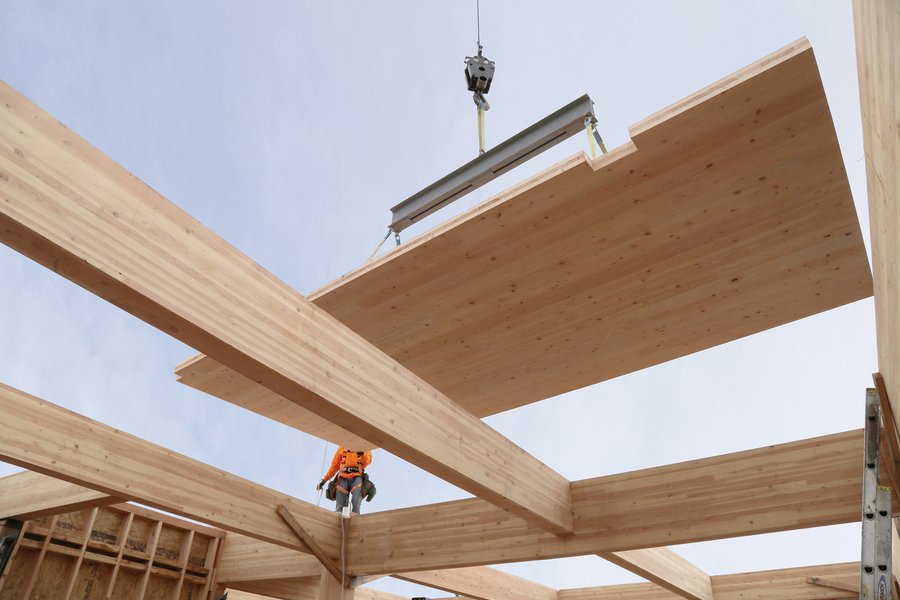
A 10' by 24', three-ply CLT floor panel is lifted into place during the construction of Albina Yard in 2016.
Video footage of the CLT installation at Albina Yard. The project's first 4,000 sf of CLT was installed in under four hours.
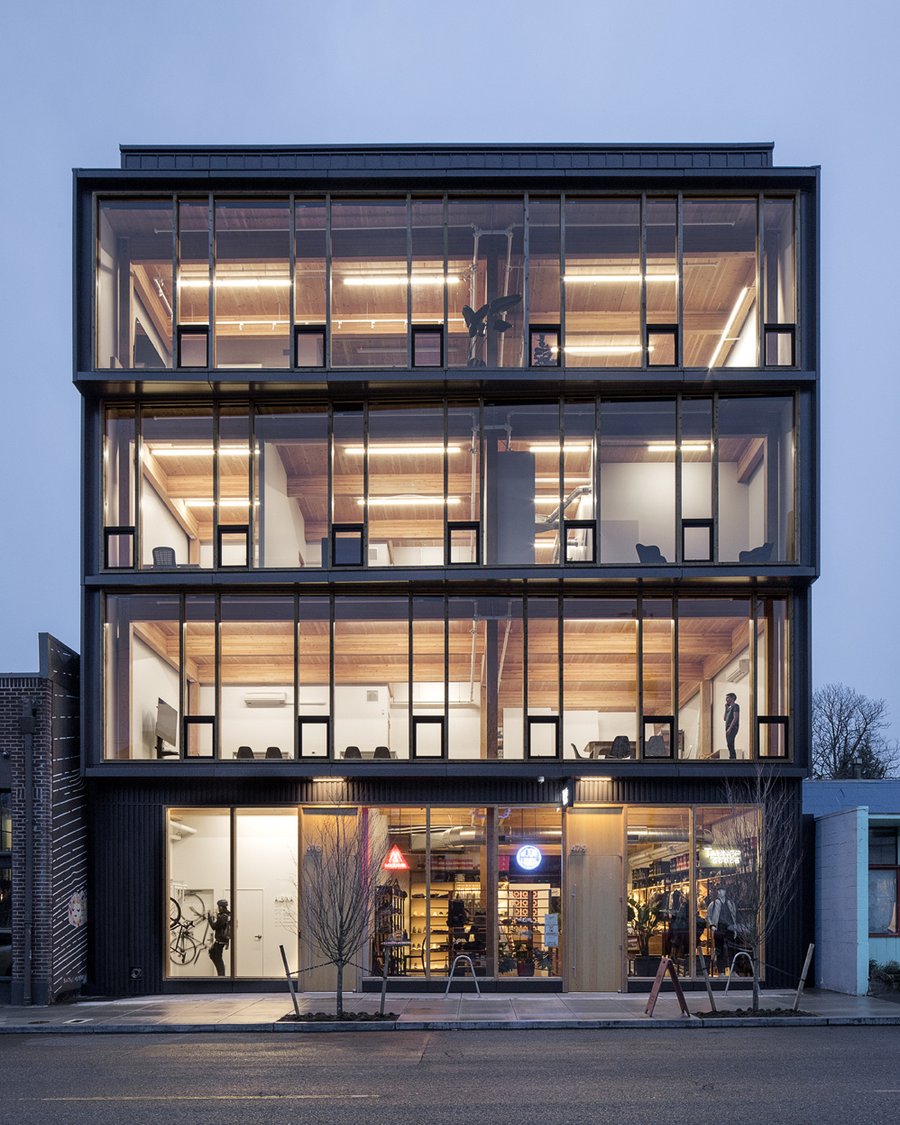